Equipment and technologies for mechanized wall plastering, pros and cons
Plastering walls, regardless of whether it is performed indoors or on the facade of a building, performs several functions. The main ones are leveling the surface and increasing thermal insulation. This mandatory stage is one of the most time consuming and time consuming. Therefore, much attention is paid to the issues of its mechanization. This article will consider the main devices for mechanized plastering of walls, the pros and cons of mechanizing the process, the application technology. And also a brief overview of the most popular manufacturers and their products is given.
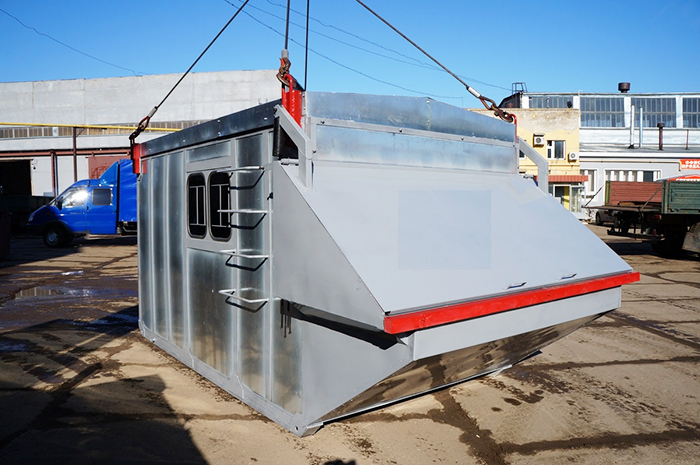
These are the plastering stations used in mass construction. Model ШС-4/6 manufactured by Remstroydormash plant
PHOTO: remstroy.info
The content of the article [Hide]
What is mechanized wall plastering
When manually applying plaster mixes to the work surface, the pressure required for adhesion between the finish and the wall is provided by the plasterer. With the mechanized (machine) method of application, the plaster mortar is supplied under the pressure necessary for uniform distribution over the surface with the creation of the required adhesion.
Most machine plastering devices use a pneumatic feeding method, but there are models based on a mechanical method of application.
Pros and cons of mechanized wall plastering
There are several technologies for the mechanical method of applying plaster.Their principle of operation, the degree of mechanization, automation of mixing processes and control of the amount of water differ significantly from each other. However, there are common advantages and disadvantages for such devices.
There are also a number of rather significant shortcomings.
Related article:
Varieties of devices for mechanical plastering
Today, craftsmen are offered a wide range of equipment for machine application of finishing materials. It can be a hand tool with a minimum degree of mechanization (hopper bucket, in other words a pneumatic shovel or a pneumatic gun) or automated plastering stations.Let's consider each of the varieties of these devices in more detail.
Hopper (pneumopath)
The hopper bucket consists of a container (3-5 l) in the lower part of which there are 4 holes through which the plaster mix is sold. Inside the bucket, opposite these holes are air nozzles. The package includes a telescopic handle with a compressed air control handle. Hose and compressor sold separately. The compressor must have a capacity of 35-45 m³ / h and a pressure of 4-6 atmospheres.
The plastering process is simple and does not require extensive prior training. The pre-mixed plaster mortar is scooped up with a ladle. The hopper is brought to the wall at a distance of 10-15 cm. After that, the compressed air supply is switched on.
Advantages:
Disadvantages:
Hopper technology: video
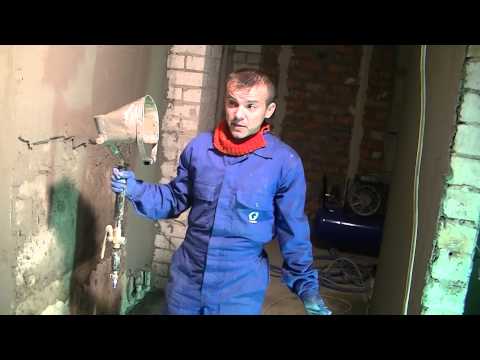
Pneumatic pistol (cartridge pistol)
Consists of one nozzle on a pistol grip, to the top of which a metal or plastic container (up to 9 liters) for plaster is attached. The principle of operation is the same as that of the hopper. Has replaceable nozzles for the nozzle (diameter 3-8 mm), which allows the use of finishing mixtures of various consistencies. It can be used not only for rough plastering, but also for decorative finishing or applying textured spray.
Advantages:
Disadvantages:
Plastering stations
They have a rather complex design. The main elements are:
According to the manufacturers' recommendations, it is rational to use such equipment in rooms with an area of at least 30 m². Immediately after completion of work, all containers and hoses for supplying the finished mixture must be thoroughly rinsed with clean water. As a rule, there are special cleaning modes, so this procedure is not too complicated and tedious.
Advantages:
Disadvantages:
Robot plasterer
This is an installation for applying plaster mixtures to flat vertical walls. The distributing part of the device moves along guides that are fixed on the floor and ceiling of the room. The robot needs to knead the plaster separately, but you can use the usual hand-applied mixes. The plant productivity is up to 80 m² / hour. The robotic plasterer cannot be used to decorate rooms above 7 m, staircases and facades.
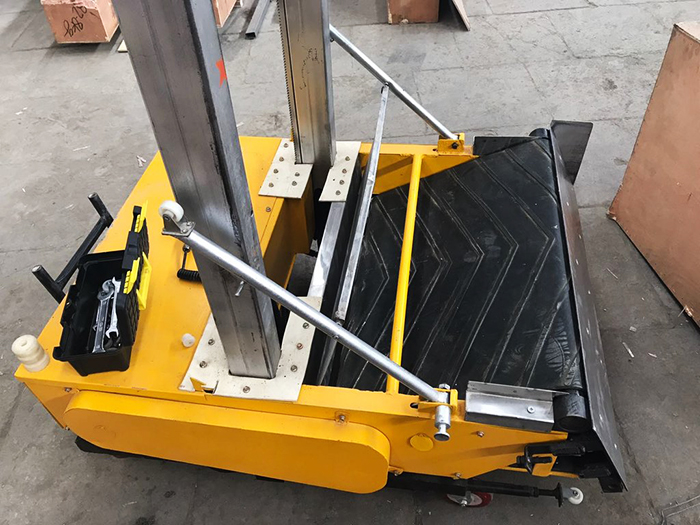
Robot plasterer, model RoboPlaster-1000, but in terms of functionality, it is rather a semiautomatic device
PHOTO: stroiformat.com
Advantages:
Disadvantages:
The process of operation of a robotic installation for plastering can be seen in the video:
Plastering disc machines are used for leveling plastered walls and ceilings both with manual and mechanized finishing. Foam or chipboard is used as trowels.
The working nozzle is connected to the power drive using a flexible shaft. This reduces vibration, making the grouting process even easier. The power drive is an electric motor with a squirrel-cage rotor, operating from a three-phase current with a voltage of 42 V and a frequency of 200 Hz. Such parameters of electricity allow the operator not to be afraid of electric shock even when working on wet and wet surfaces.
There are two main types of plastering machines:
- Single disc. For example, SO-112B, the circle rotates in one direction.
- Two-disk. For example, SO-86B. It has two circles, an inner and an outer (in fact, a ring), which rotate in different directions.
The process of grouting plaster is perfectly illustrated by the proposed video:
The process of preparing installations for mechanized plastering for operation may differ significantly depending on the type of device. However, there are general rules and recommendations that must be followed, these are:
- Preparation of the base.
- The sequence of the plastering process.
- Grout - leveling the coating.
Preliminary surface preparation
Preparation of the surface of walls and ceilings for plastering using mechanical means practically does not differ from ordinary measures:
- The surface of the base is cleaned from dirt and dust. Old trim is removed if necessary.
- Metal embedded parts are treated with anti-corrosion properties.
- Irregularities and defects are corrected if their relief exceeds 1.5-2 cm.
- The base material is treated with an appropriate primer.
- Concrete (and other dense materials) - by concrete contact.
- Porous and hygroscopic - deep penetration primer.
- If necessary, beacons are installed, along which alignment is carried out.
The process of applying the plaster mixture to the warp
Based on the practical recommendations of operators and manufacturers, the following list of operating rules for plastering stations was compiled:
Aligning the finish
The final stage of any plastering is the formation (leveling) of the treated surface. The easiest and fastest way to level the surface is by focusing on the beacons. The optimal processing time is not earlier than 20-30 minutes after application, but not later than 50-60 minutes. The exact time depends on the type of mortar, layer thickness and manufacturer's recommendations. Various tools can be used for alignment:
The alignment process requires special attention in the corners and at the joints.
Leading equipment manufacturers and their products
PFT. German manufacturer of plastering stations, whose products have proven themselves in the market.The most successful models are PFT G4 Smart and RITMO XL (new series of equipment). Despite the fact that the performance of comparable models of both series practically does not differ, the station of the PFT series is almost twice as large. The equipment operates from both single-phase and three-phase networks, there are also multi-voltage models (220V / 380V). Almost all reviews for the products of this manufacturer are positive, so if the high price does not scare you, then it is better to purchase them. Price range 250-300 thousand rubles.
Putzmeister. Another German manufacturer that has been producing construction equipment, including plastering stations, since 1958. In terms of functionality and cost, its models practically do not differ from the PFT series.
NOVO. Company headquarters registered in Germany, manufacturing facilities in China. Despite this, the products are distinguished by their reliability and high performance. Price range 200-250 thousand rubles. In addition, there are additional advantages in the design:
Typhoon. Plastering station from a domestic manufacturer of the same name from Stavropol. The equipment is an extremely simplified and extremely unfortunate replica of the PFT Ritmo L-L4-2. Of the main disadvantages, users name:
Other plastering stations of domestic production that can be found on the equipment market: Meteor, VEK, TSM 2, Hermes are even less successful copies of Typhoon.
Gallery: manual tools for small mechanization of applying plaster mixes:
- PHOTO: myshtukaturka.ru
- PHOTO: i.ytimg.com
- PHOTO: otdelka-expert.ru
- PHOTO: couo.ru
Summing up
Which is better hand or mechanized wall plastering? There is an unequivocal answer to this question - it is better to mechanize the process of plastering and grouting. At the same time, the choice of hand-held devices and plastering stations in the modern construction equipment market allows them to be purchased by both professionals and home craftsmen.