Homemade metal lathe with your own hands
If you assemble a home-made metal lathe with your own hands, you can get at your disposal functional equipment for metal processing at no extra cost. For objectivity, we will consider not only the assembly process, but also the current offers of the finished product market. The information below will help you make a correct comparative analysis, taking into account financial capabilities, professional skills and other personal characteristics.
The content of the article [Hide]
- 1 What can you do with a homemade metal lathe with your own hands
- 2 What a lathe consists of
- 3 Making a metal lathe with your own hands: step-by-step instructions with comments
- 3.1 The first stage: selection of a metal lathe device, preparation of project documentation
- 3.2 How to find the right motor for your lathe
- 3.3 Assembly order
- 3.4 How to make a lathe with your own hands from a drill
- 3.5 Video: lathe in 15 minutes
- 3.6 Features of creating a lathe for metal with your own hands
- 4 How you can upgrade a lathe yourself
- 5 Features of work on homemade lathes
- 6 Safety when working with a homemade lathe and proper care
- 7 Market offers of lathes for metal: varieties, prices, additional equipment
What can you do with a homemade metal lathe with your own hands
With the help of a table metal lathe, you can quickly and efficiently perform various working operations:
Study carefully the materials in this article.If it is difficult to implement the project with your own hands, knowledge will be useful for an objective assessment of the range of specialized stores. In separate sections there is information about operating rules that will help to extend the service life of technological equipment and provide a high level of safety.
What a lathe consists of
Even a small lathe weighs a lot, creates vibrations during operation. A reliable base (1) is required, on which functional units and individual parts are fixed. If it is planned to create a floor version, use reliable supports of the required length. The final height of the work area should be user-friendly.
Other components are listed in the following list:
Lathe support
Drawing Notes:
In a detailed study of this part of a metal lathe, it is necessary to take into account the increased loads to which it is subjected in the process of performing technological operations. It is necessary to pay attention to the large number of moving components.
Sturdy parts are not enough to maintain precision. Constant adjustments will help eliminate backlash to compensate for wear. It is recommended to replace damaged seals with new products.
Tailstock
Hereinafter, we will consider projects that are simple for self-reproduction with clarifying comments. The example in the figure is more suitable for woodworking equipment... To work with strong workpieces for a long time, you should make a support shoe from a steel plate.
With their help, the basic capabilities of the tailstock are expanded. In the author's recommendations, it is proposed to remove part of the standard holder of the cartridge (3). This will increase the working stroke of the tool, process larger workpieces.
Features of making do-it-yourself headstock of a lathe
A belt drive (1) is used here, which is characterized by low cost, low noise level. A double pulley (2) is installed for stepping the torque. To extend the life of the spindle (3), a pair of ball bearings must be used. If necessary, holes are made in the housing for periodic filling of grease.
These clamps are automatically centered without additional adjustment.Self-manufacturing of such units will cause difficulties. Therefore, this functional element of the headstock of a lathe can be bought in a store.
How to make a tool holder for a lathe with your own hands
This will allow you to make repairs without unnecessary difficulties. Screws are screwed into the threaded holes, which firmly fix the tool. The distance between the plates is determined taking into account the size of the cutters.
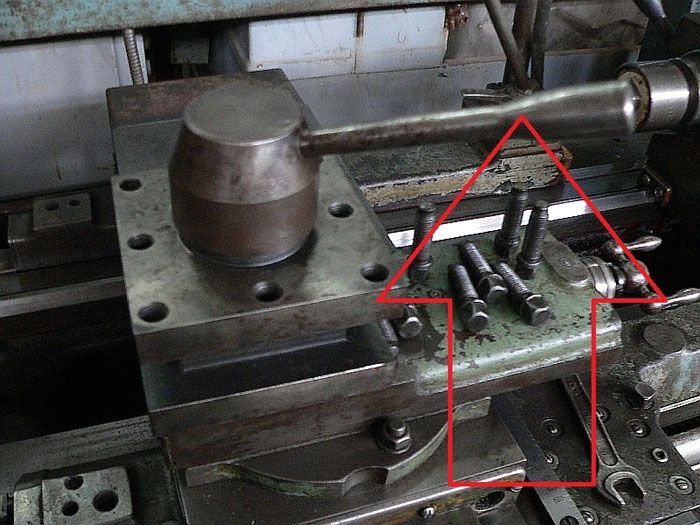
A handle is installed on top for quick rotation of the assembly. This device allows you to quickly change tools for complex sequential processing of workpieces
Making a metal lathe with your own hands: step-by-step instructions with comments
The first stage: selection of a metal lathe device, preparation of project documentation
The following drawings show the completed project. Such a relatively simple metal lathe for a garage (workshop) is not too difficult to make on your own. Belts and some other components are standard items. Other parts can be made by yourself or ordered in a specialized workshop.
To select the required accuracy of movement of the caliper, the lead screw thread pitch is changed. It is cut into a die on a screw-cutting machine. To strengthen the structure, connections are made using welding. Headstock bodies are made from a channel (# 12/14).
How to find the right motor for your lathe
The project presented above is designed for the use of a power unit with a capacity of 450-600 W with a maximum rotational speed of the working shaft - 2500-3500 rpm.
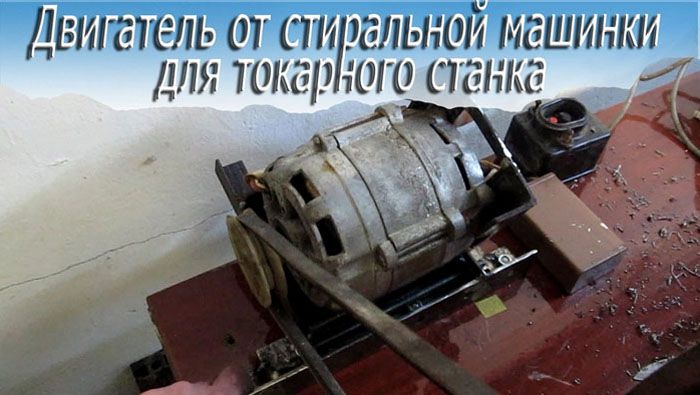
In order to save money, some authors of projects use old electric motors from out-of-order household appliances
Such solutions are quite suitable if you choose a working engine of sufficient power.
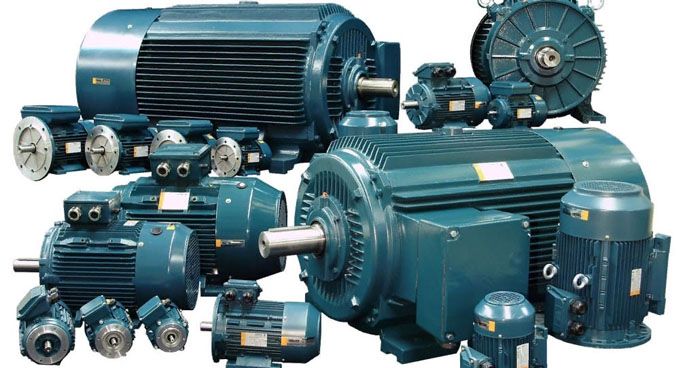
The reasonable cost of products in this category allows you to easily find an acceptable option in the retail network. In this case, you can count on the official manufacturer's guarantees.
In order not to be mistaken, you can study examples of factory machine tools for metal, successful homemade products. Based on such a mini-study, it is easy to conclude about the following proportions: for processing parts with a diameter of 8-12 cm and a length of 60-80 cm, electric motors with a power of 600-800 W are used. Standard air-cooled asynchronous type models are suitable. Collector modifications are not recommended. They sharply increase the speed when the load on the shaft decreases, which will be unsafe. To prevent such situations, you will have to use a reducer, which will complicate the design.
One advantage of the belt drive should be emphasized. It prevents direct mechanical impact on the shaft from the tool in the transverse direction. This extends the life of the support bearings.

Assembly order
This algorithm explains the sequence of actions when working with the above drawings. The use of other design documentation implies the introduction of appropriate changes in the assembly process.
They start with the headstock. A spindle is installed in it. Further, the entire unit is connected to the running pipe using bolting. Pre-thread is cut on the parts of the fastening.When performing this operation, carefully control the alignment of the parts.
At the next stage, a power frame is assembled from the channels. When the frame is made, the headstock is installed on it. Here, too, the parallelism of the running tube and the long frame parts must be carefully checked. Make the markup exactly. The holes are drilled sequentially with an additional reamer bore, checking each attachment point. One or two mistakes will not unduly compromise the durability of the channel, so it is better to make a new exact hole in a different place, if necessary.
When assembling this unit, special attention should be paid to the accuracy of the placement of the central axes of the spindle (1) and quill (2). If a mistake is made, conical surfaces will be obtained instead of cylindrical when machining workpieces. Also check the parallelism of these elements to the running pipe. The support bar (3) prevents the tailstock from unfolding. For height adjustment, steel spacers can be used.
Caliper parts are installed sequentially in accordance with the assembly drawing diagram. A particularly high precision is not needed here, since numerous adjustments are provided. If intensive use is expected, make individual units detachable in order to replace wearing parts at no extra cost.
At the final stage, an electric motor is installed, connected to the mains according to the selected scheme. They check the functionality of a metal lathe with their own hands in practice. To improve the appearance and protect against corrosion, some parts are coated with primer and paint.
How to make a lathe with your own hands from a drill
For processing wood blanks, plastic, other soft materials, the power of a typical household power tool is quite enough. This example shows how to make a functional machine with your own hands in 15-20 minutes. With the help of the last photos, the table tells about the creation of an improved design:
Video: lathe in 15 minutes

Features of creating a lathe for metal with your own hands
The previous chapter told about the simplest designs that will help make a lathe from a drill using inexpensive materials at hand. In some cases, even detailed drawings are not needed. This approach is sufficient when working with wooden blanks, when high precision is not required.
Related article:
But it will not work if you need to create a metalworking lathe with your own hands. The video demonstrates not only the potential capabilities of high-quality equipment in this category, but also the tasks solved by the author of the project:

How you can upgrade a lathe yourself
The above drawings are a time-tested project. With their help, you can make a functional mini lathe for metal with your own hands. But some modern improvements will be appropriate:
Features of work on homemade lathes
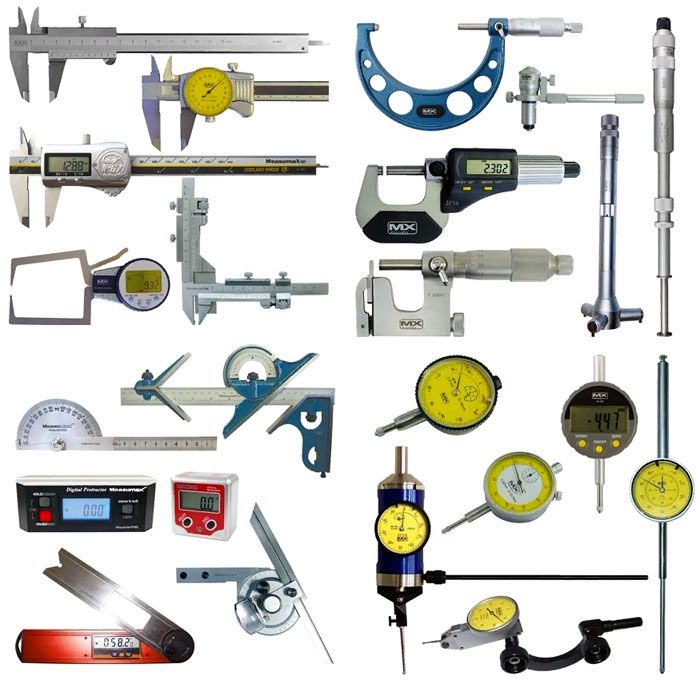
To control and obtain the required level of accuracy, mechanical and electronic calipers, calipers, and other specialized measuring instruments are used.
Mastering metal processing is a topic for a separate article. To obtain the desired result, take into account the toughness and brittleness, other characteristics of the metal and working edges. The technology is optimized taking into account the rotation speed of the workpiece, temperature conditions.
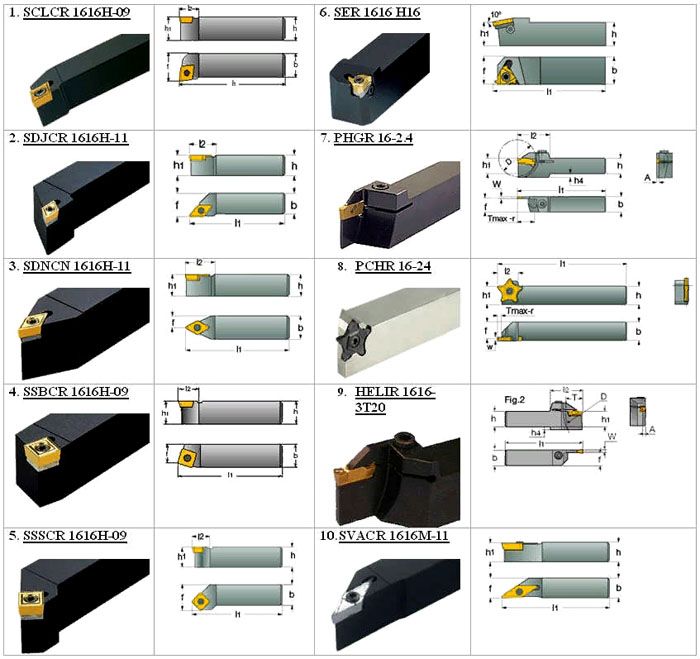
For external and internal turning, cutting, threading and other operations, different types of cutters are used
Metal turning video (advice from an experienced craftsman):
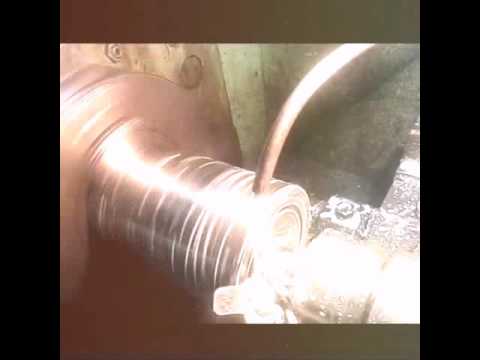
Safety when working with a homemade lathe and proper care
After assembly, it is necessary to make sure that there are no faults before connecting to the network. Check the free rotation of the spindle, the absence of delays during the operation of the drive mechanisms and extraneous noise. Alignment is closely monitored. It is necessary that the parameters of the power supply network correspond to the needs of the power unit in the mode of maximum power consumption, when switched on.
Before starting work, make sure the presence (serviceability) of protective screens, covers. The new tool is installed with the electric motor stopped using all standard fasteners. Observe the processing modes corresponding to the parameters of the cutters and the workpiece.
After the completion of working operations, waste is removed. Lubrication and other work stipulated by the maintenance schedule are timely performed.
Market offers of lathes for metal: varieties, prices, additional equipment
You should carefully evaluate the process of creating a homemade lathe with your own hands. Taking into account the real costs, it can turn out to be less economical than purchasing a finished product. Accurate conclusions can be drawn only taking into account real conditions. In any case, personal implementation of the project implies the potential for creating equipment with unique technical characteristics.
Submit your feedback on this topic in the comments to this article. This information platform is completely free to use.